Using industry-standard design process, we collaborate with the customer to understand the needs of the finished product. We work to ensure there is clarity on the design tolerances, highlighting any clashes with other components on the overall result. We confirm the type and level of finish required and, through that process, identify the visible surfaces to ensure the result is aesthetically correct and the agreed finish will be fit for purpose. We ensure the customer approves the final drawing with detailed tolerances and specific details before we develop the die.
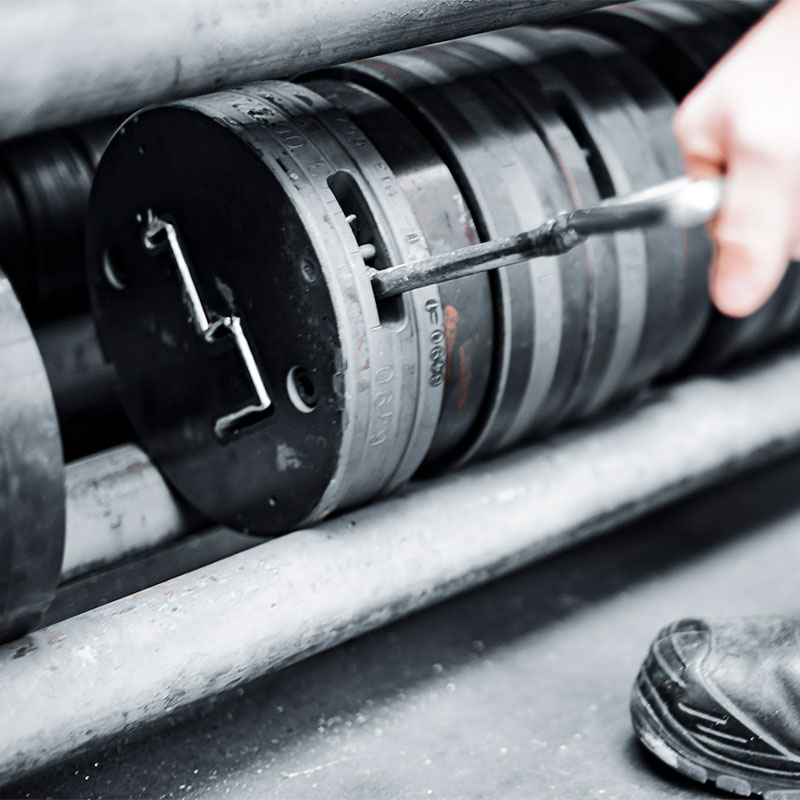
Design Turnaround
Once the sample is approved, initial delivery can be completed in as little as 5-10 days. To achieve precise die performance with complex shapes, multiple iterations may be required, which is reflected in the design costs.
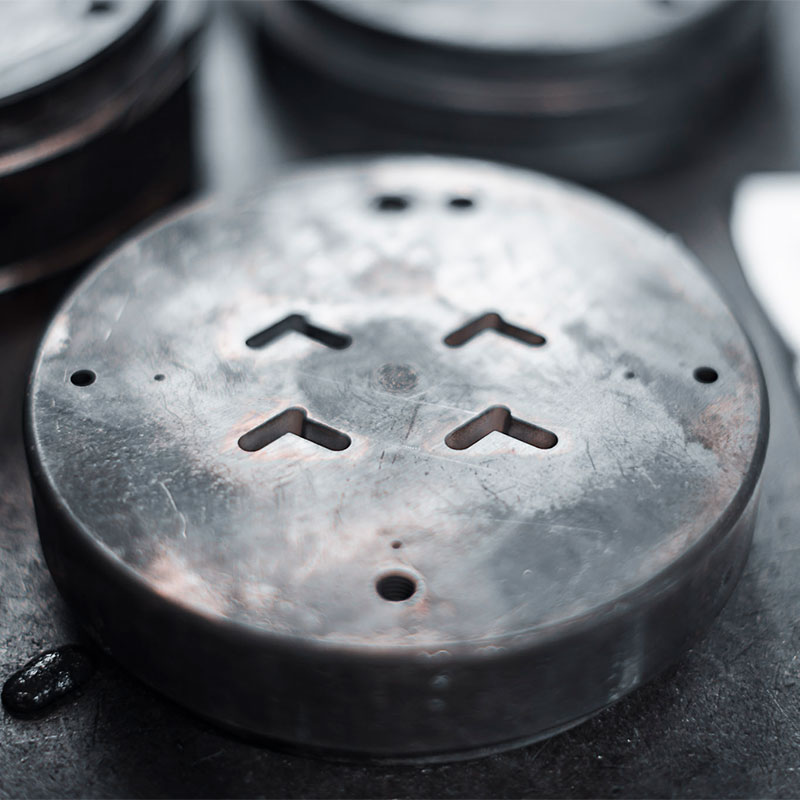
Die Wall Consistency
Keeping the wall thickness consistent and above 1.2mm makes profiles more efficient to extrude, keeping costs down. Avoiding sharp corners and using radii of .3mm or larger aid in making a die efficient to run.
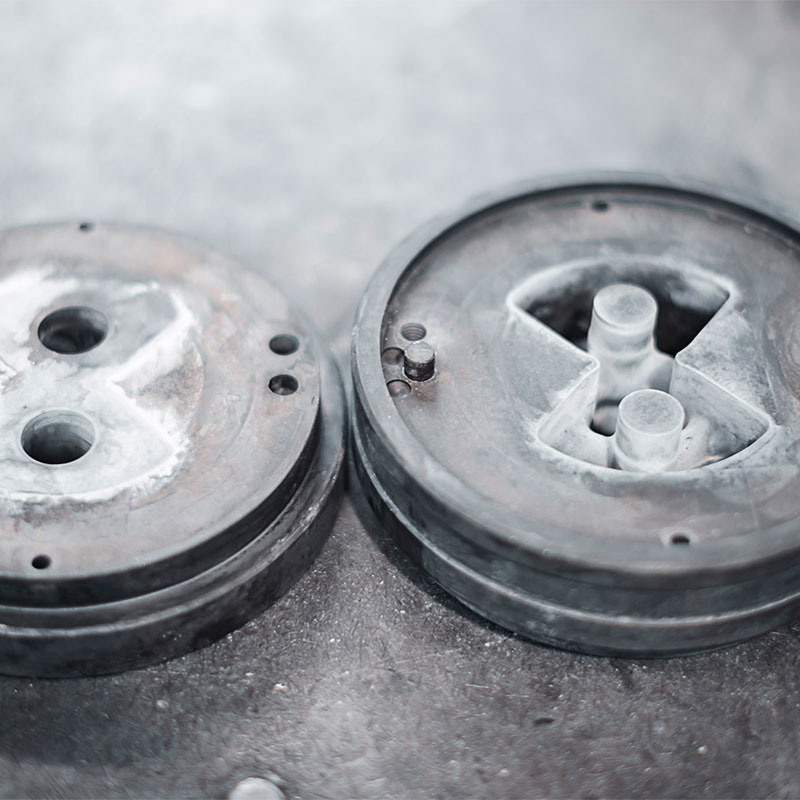
Complex or Multiple Hollow Profiles
Multiple hollows within a profile make a die more expensive to manufacture and extrude, hence subsequent extrusion costs will be higher.
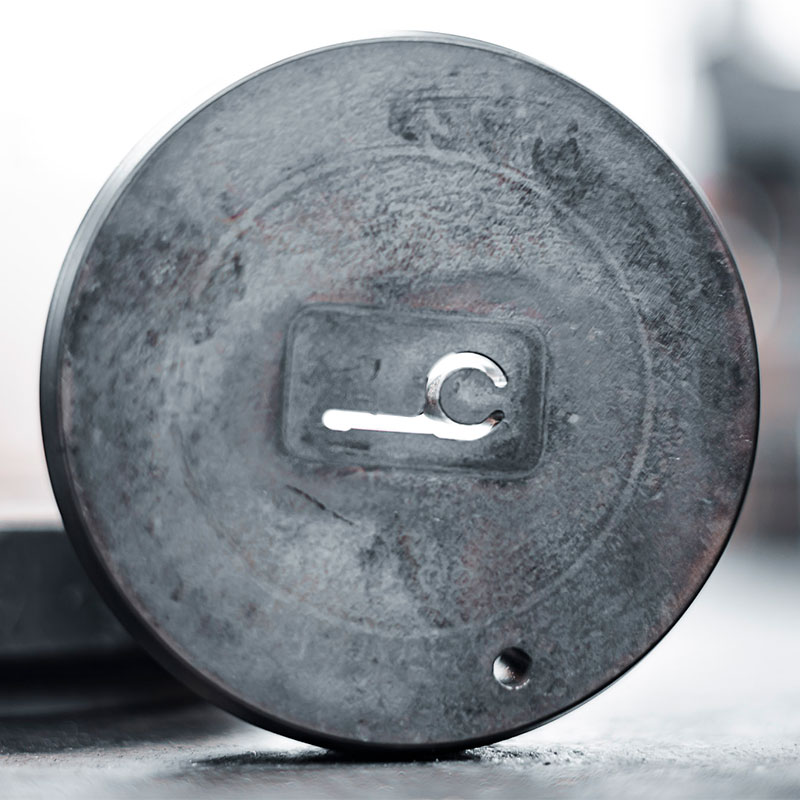
Design Modifications
Once a die is manufactured, it cannot be modified. Changes to a design will require a new die. We can provide 3D printed samples for evaluation before the die is manufactured.
Cost of die varies between $1000-$4000+
The cost of dies can vary depending on design complexity and size (profile size limits are roughly 160mm wide and 100mm diameter).
Initial cost of dies: we generally postdate the invoice by 12 months and credit back the die if a certain volume is achieved as its output.